Push Back Racking System
Our Push Back Racking System is designed to maximize warehouse space while ensuring easy and efficient storage of goods. Ideal for high-density storage, this system allows pallets to be stored on inclined rails, pushing back the previous pallets as new ones are loaded. It is a highly adaptable solution, offering optimal storage capacity and easy access to goods. Available in various sizes and configurations, our Push Back Racking is perfect for industries in Saudi Arabia and beyond. As a trusted push back pallet rack manufacturer, we provide durable and reliable racking systems tailored to meet your warehouse needs.
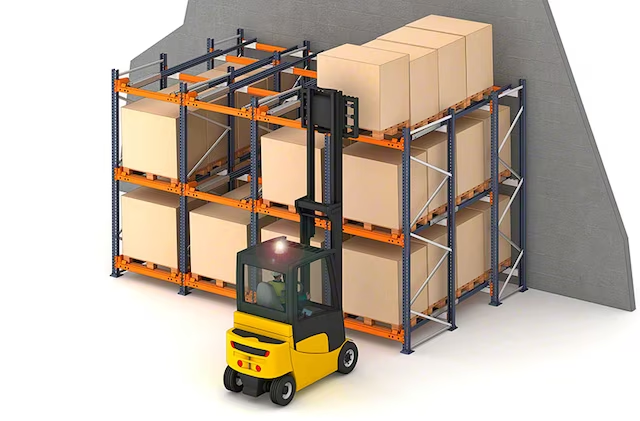
Push Back Racking System – Ideal for Efficient Storage Solutions in Saudi Arabia and Beyond
A Push Back Racking System is a highly efficient and space-saving solution designed for warehouses and distribution centers. Ideal for businesses in Saudi Arabia, including cities like Dammam, Riyadh, and Jeddah, as well as regions such as the UAE, Qatar, Kuwait, and Jerusalem, this system offers numerous benefits. Here are the key advantages of Push Back Pallet Racking:
- Maximized Storage Density: Push back racks allow for a higher number of pallets to be stored within a smaller space, boosting storage capacity by reducing aisle space.
- Improved Inventory Management: With the ability to store pallets by depth, items are more easily accessible, streamlining order picking and reducing time spent searching for products.
- Increased Safety: Push back racking systems reduce the need for forklifts to navigate narrow aisles, minimizing accidents and improving overall safety in the warehouse.
- Flexible Configuration: The system can be customized to fit various pallet sizes and weights, making it suitable for businesses with diverse storage needs.
- Reduced Handling Time: The innovative design of the push back system enables faster loading and unloading, improving operational efficiency and reducing labor costs.
- Cost-Effective: By increasing storage capacity and improving workflow, push back racking systems offer a long-term investment that can help businesses save on operational costs.
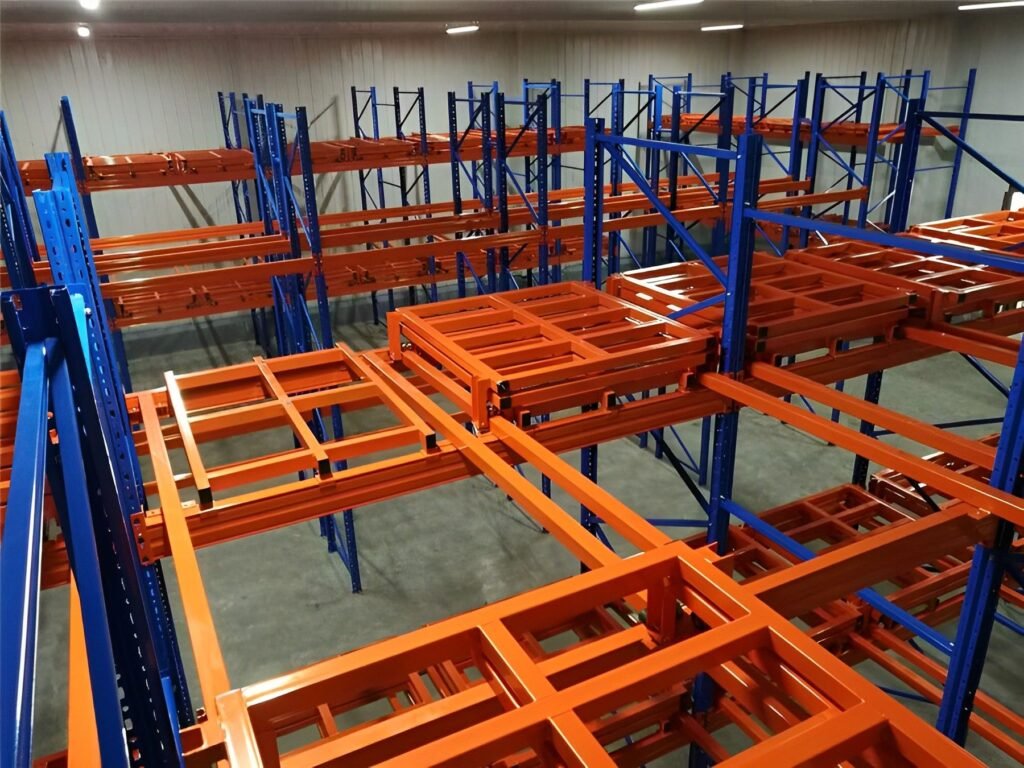
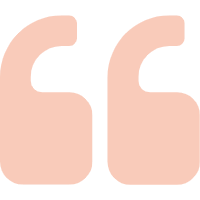
In addition to being highly practical, these racks have removed the need for aisles and simplified storage tasks.
APPLICATIONS OF PUSH-BACK PALLET RACKING
Push-back racking finds its ideal application in various warehouse scenarios:
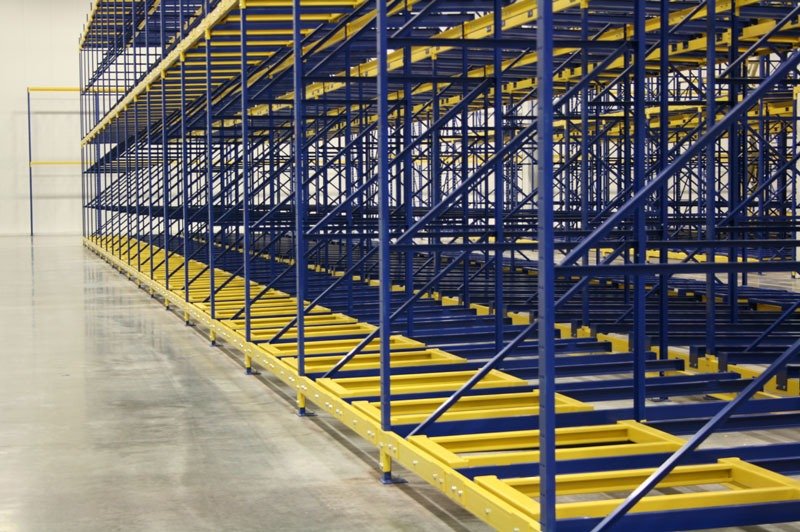
Medium-turnover Product Warehouses
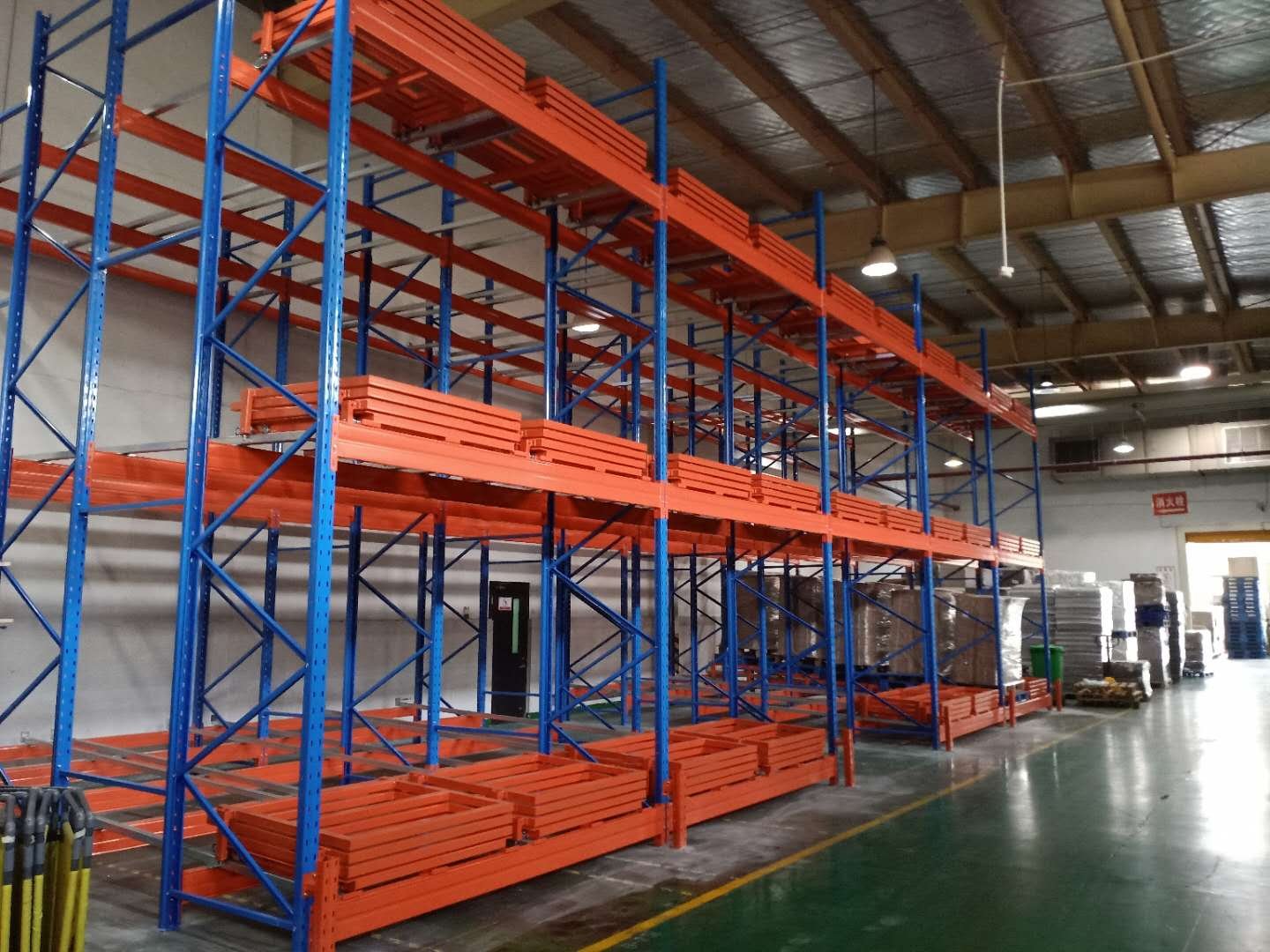
Batch storage
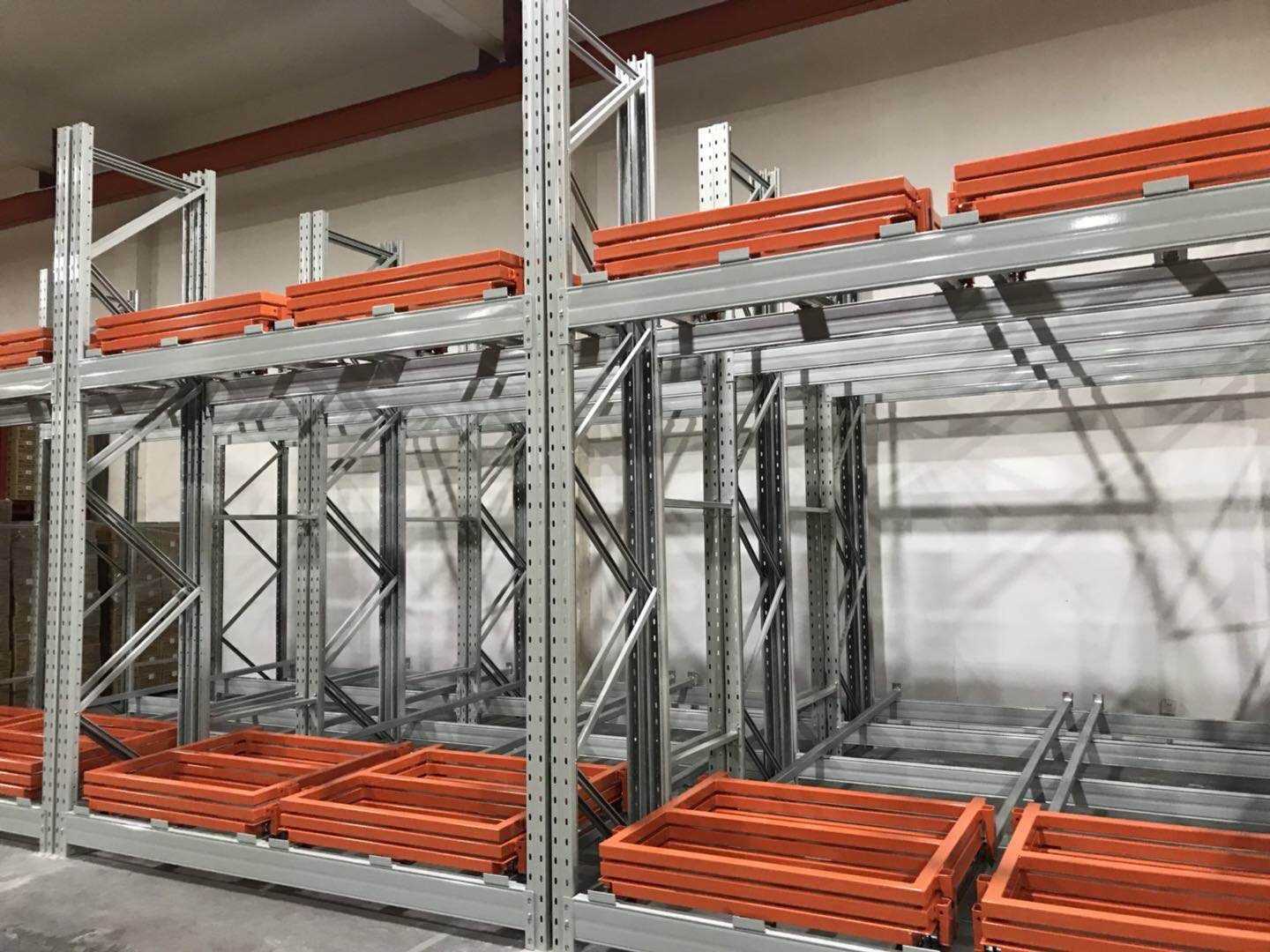
Cold Storage Facilities
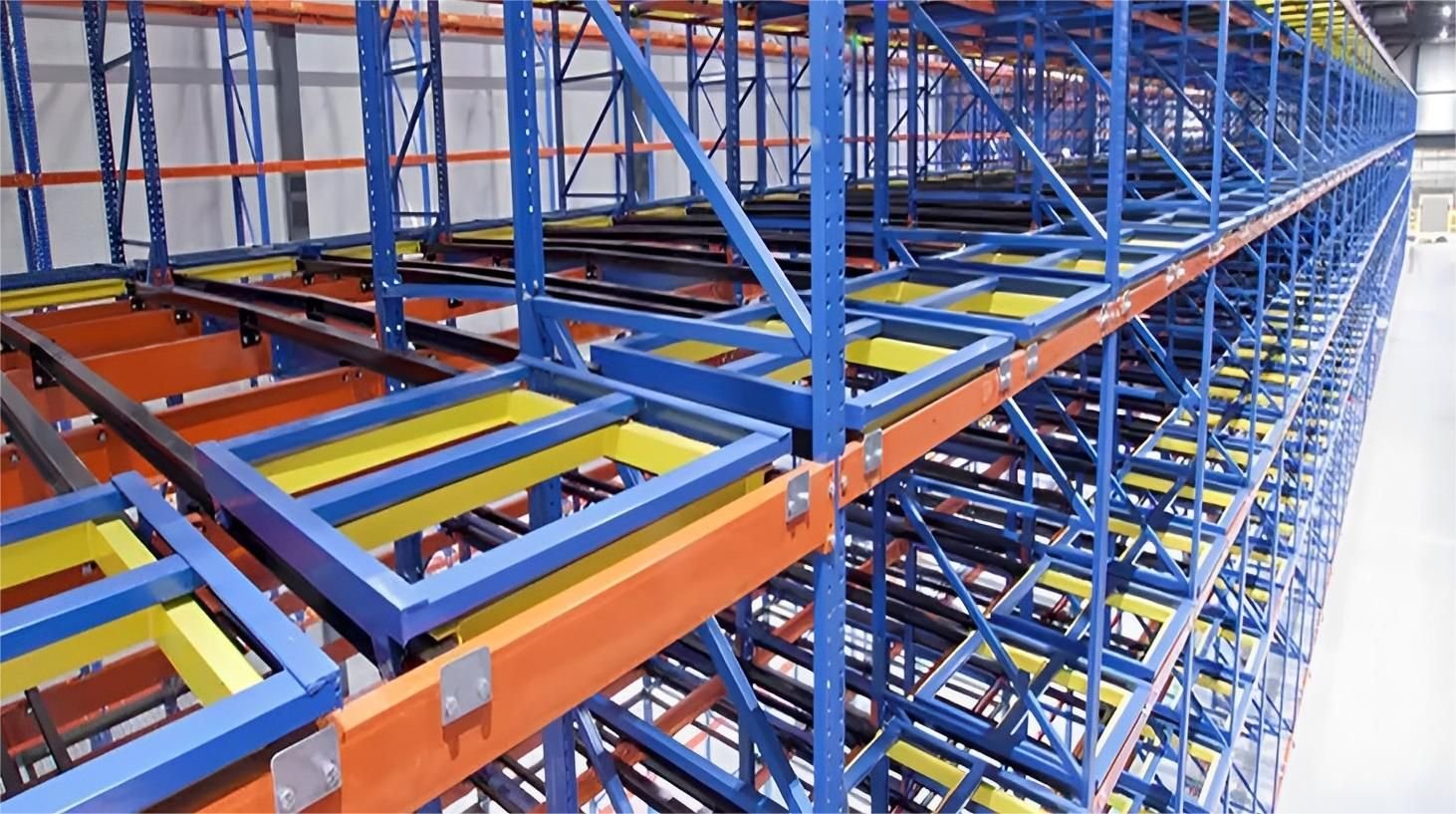
Temporary Storage for Orders
COMPONENTS OF PUSH-BACK PALLET RACKING SYSTEMS
Push-back racking is the perfect system for companies with medium-turnover palletised goods or with a small variety of SKUs and few pallets per SKU. It is also ideal for facilities that need to leverage their available surface area.
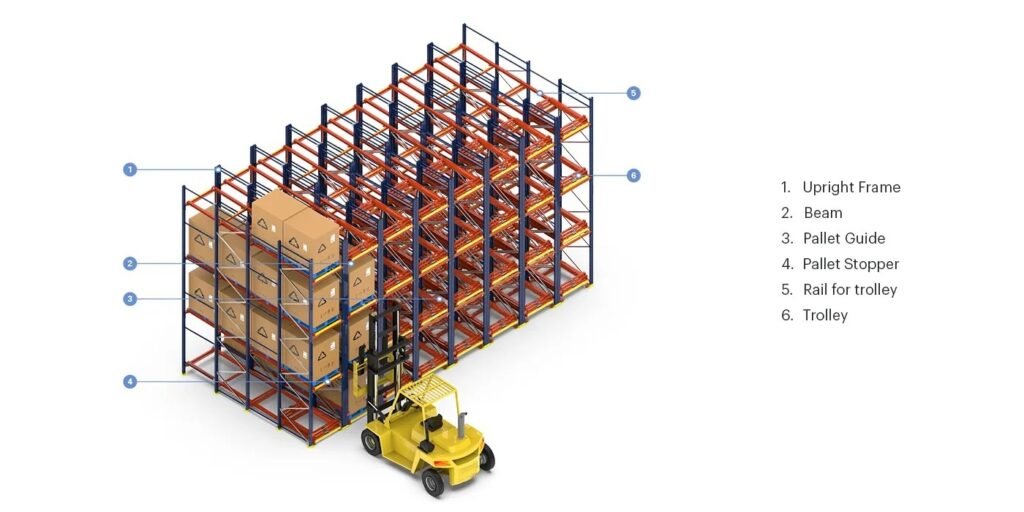
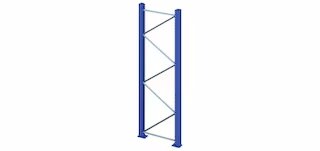
FRAMES
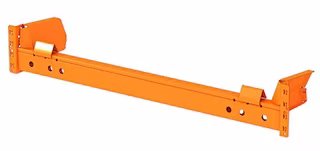
BEAMS
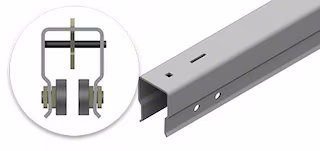
CARTS
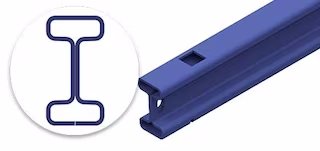
RAILS
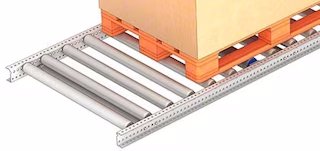
ROLLERS
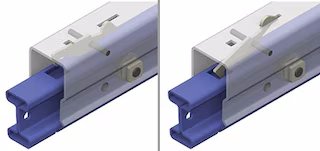
LOCK TRIGGER
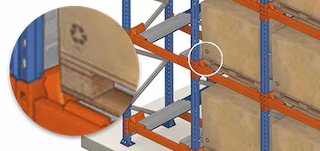
PALLET CENTRALISERS
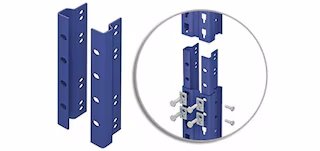
CART OCCUPANCY INDICATORS
FAQS
The Characteristics of Push Back Racking:
- Push Back Racking is a high-density pallet racking system that allows pallets to be stored and retrieved easily. It works by using a series of carts that move backward when new pallets are added, enabling you to store multiple pallets in a single location, improving storage efficiency.
- The Push Back Racking system uses carts mounted on rails to allow pallets to “push back” as new pallets are added. As pallets are retrieved from the front, the remaining pallets roll forward, making it easy to access products in a last-in, first-out (LIFO) order.
Push Back Pallet Racking features include high-density storage, efficient space utilization, easy access to products, and the ability to store different types of goods. It provides excellent control over inventory, and its dynamic system improves operational efficiency.
- The main benefits of Push Back Racking are its ability to increase storage capacity, improve organization, and reduce retrieval times. It allows for higher-density storage and reduces aisle space requirements, making it ideal for large warehouses in Saudi Arabia and the UAE.
- Unlike conventional pallet racking systems, Push Back Warehouse Racking enables pallets to move on inclined rails, which allows for higher density storage. This makes it ideal for warehouses in Riyadh, Dammam, and other locations in Saudi Arabia that need to maximize their available space.
Push Back Pallet Rack Systems are available in different configurations and can handle varying load capacities depending on the requirements. These systems can support heavy-duty loads and provide flexible solutions for different types of inventory, from small to large pallets.
- Yes, Push Back Racking is ideal for high-velocity operations as it allows for faster turnover of goods. With multiple pallets stored per lane, items can be retrieved and replaced quickly, which helps optimize operations in busy warehouses, especially in places like Dubai and Qatar.
- Yes, Push Back Pallet Racks are relatively easy to install, though professional installation is recommended for the best results. The system is designed to be flexible, which makes it an excellent choice for growing businesses in Saudi Arabia and beyond.
Absolutely. Push Back Racking can be customized to fit various warehouse sizes and configurations. Whether you’re setting up a warehouse in Kuwait, Jerusalem, or Riyadh, the system can be tailored to meet specific storage needs.
- Push Back Racking systems are designed with several safety features, including safety brakes, sturdy rails, and locking mechanisms. These features help prevent accidents and ensure the stability of the racks when in use.
The Uses of Push Back Racking:
- Push Back Racking is mainly used to store goods in a warehouse, especially for items that need to be accessed in a last-in, first-out (LIFO) order. It’s commonly used in industries like food storage, retail distribution, and logistics across Saudi Arabia, the UAE, and Qatar.
- Push Back Pallet Racking maximizes storage density and minimizes the need for wide aisles. This allows for more efficient use of warehouse space, particularly beneficial for businesses in cities like Riyadh, Dammam, and Tel Aviv that require higher storage capacity.
Yes, Push Back Racking can be used for perishable goods, especially in warehouses that need to adhere to LIFO inventory practices. This makes it ideal for food storage businesses in Saudi Arabia and the UAE.
Since Push Back Pallet Rack Systems allow for pallets to move without needing a forklift to manually shift them, this significantly reduces forklift traffic in the warehouse. This is a huge advantage in busy warehouse environments in Dubai and Qatar.
Yes, Push Back Racking is highly versatile and can be implemented in both small and large warehouse spaces. It’s a great choice for maximizing storage in warehouses across various regions, including Saudi Arabia, Kuwait, and Jerusalem.
Push Back Pallet Rack Systems are beneficial for industries such as retail, manufacturing, food storage, pharmaceuticals, and more. These industries are prominent in countries like Saudi Arabia and the UAE, where efficient warehousing is critical.
- Yes, Push Back Racking is ideal for storing seasonal stock. It allows for quick and easy access to seasonal goods, helping businesses in Saudi Arabia and Dubai efficiently manage inventory without wasting valuable space.
Push Back Racking systems enhance inventory management by providing better organization and efficient retrieval. This is especially useful for large-scale operations in locations like Riyadh and Dammam, where managing large volumes of stock is critical.
Yes, Push Back Racking is designed to support heavy loads. It’s commonly used to store heavy-duty items such as machinery and industrial products in warehouses across Saudi Arabia and other GCC countries.
- Push Back Racking allows pallets to be stacked more efficiently and accessed from the same aisle, which increases storage capacity without requiring additional warehouse space. This makes it an excellent solution for warehouse operations in cities like Tel Aviv, Kuwait, and Dubai.
RELATED PRODUCTS
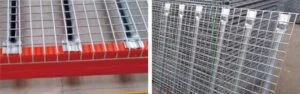
WIRE MESH DECKING
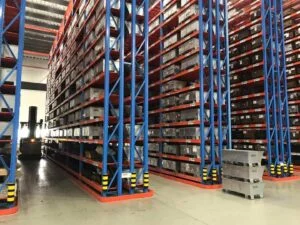
VNA RACK :VERY NARROW AISLE RACKING
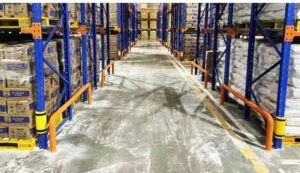
RACK UPRIGHT PROTECTOR
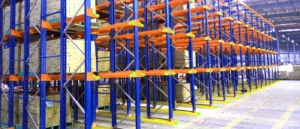
DRIVE-IN RACKING
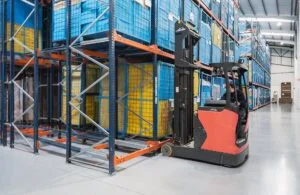
PUSH-BACK RACKING
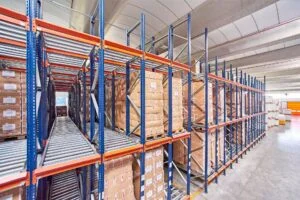
PALLET FLOW RACKING
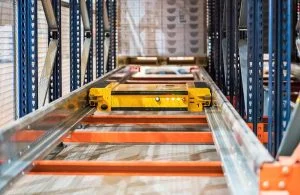
SHUTTLE RACKING
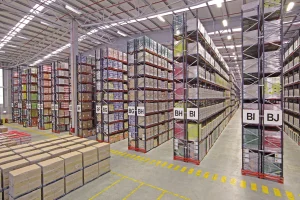