Our Long Span Shelving System is a robust and versatile storage solution designed for heavy-duty applications. Perfect for use in warehouses, factories, and retail environments, this racking system offers adjustable shelves that accommodate a wide range of items, from small parts to large, bulky goods. Constructed with high-quality steel, Long Span Racking ensures durability and stability, even under heavy loads. This system is highly customizable, allowing for easy expansion as your storage needs grow. Available across Saudi Arabia, our Long Span Shelving is the ideal choice for efficient and organized storage in any space.
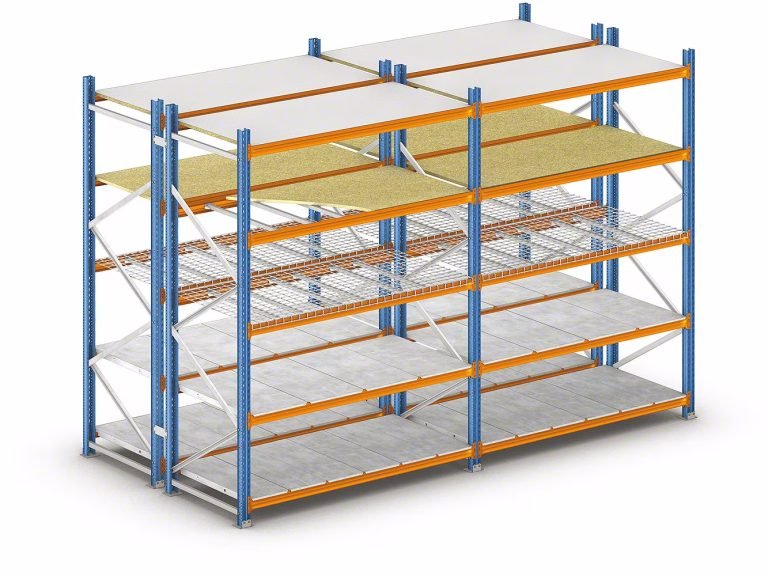
Long Span Shelving Systems – Reliable and Efficient Storage Solution
Key Benefits of Long Span Shelving:
- Enhanced Load Capacity: Long span racking systems are designed to carry heavy loads, making them ideal for storing bulky items, industrial materials, and goods of varying sizes.
- Flexible Storage Options: With adjustable shelf heights and depths, long span shelving provides customizable storage solutions that adapt to your unique needs.
- Maximized Space Efficiency: The ability to store items both vertically and horizontally ensures that your storage space is utilized efficiently, reducing clutter and maximizing warehouse capacity.
- Easy Assembly and Installation: Our long span racking systems are simple to assemble and install, saving you time and effort during setup.
- Durable Construction: Built with high-quality materials, these racking systems are engineered to withstand heavy-duty use, offering long-lasting reliability for your storage needs.
- Cost-Effective Solution: The robust design of long span shelving means fewer repairs and replacements, providing businesses with a cost-effective, long-term storage solution.
Maximize your storage space today with Long Span Shelving Systems from Suhong Storage Rack.
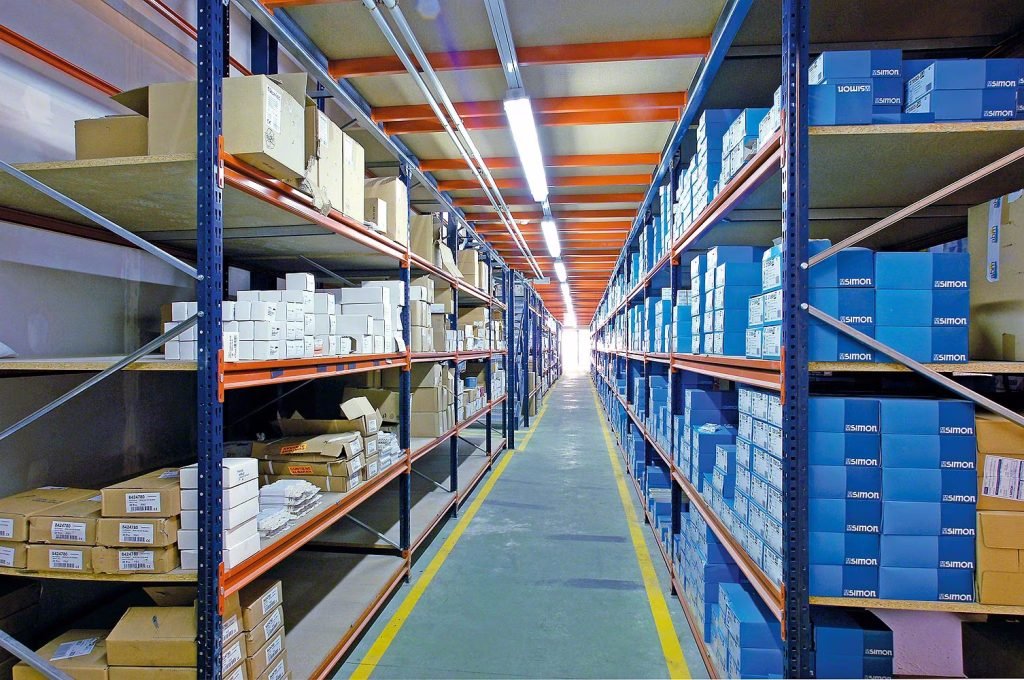
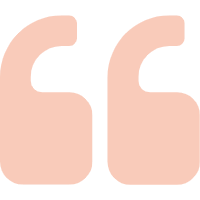
In addition to being very practical, with these racks, we’ve eliminated aisles and streamlined storage tasks
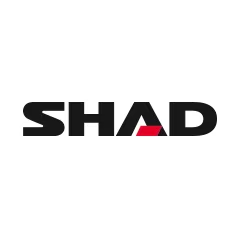
Marina Xicola
Operations Manager
SHAD
(Barcelona, Spain)
Long Span Shelving
Long Span Shelving is an extremely flexible solution, providing customizable storage options for various goods and heavy-duty items.
Long Span Shelving is a versatile and durable storage solution designed to hold heavy and bulky items. Ideal for warehouses, factories, and retail environments, it offers adjustable shelves for maximum space efficiency. Commonly used in regions like Saudi Arabia, UAE, and Qatar, it enhances organization and accessibility in storage areas.
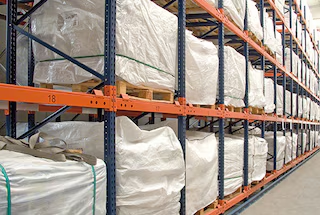
Warehouses with medium-turnover products
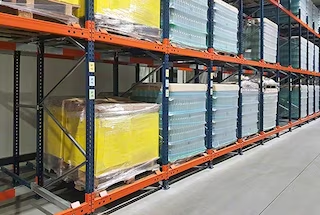
Batch storage
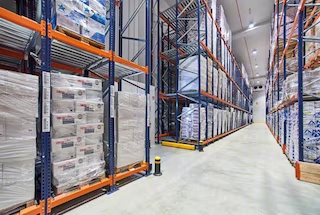
Cold stores
FAQS
Characteristics of Long Span Shelving
- Long Span Racking is a robust storage solution designed to store heavy-duty items and large loads. It consists of vertical frames and horizontal beams that provide durable shelving. It’s commonly used in warehouses and storage areas in Saudi Arabia, especially in cities like Riyadh and Dammam.
- The Long Span Shelving System offers easy access to goods, flexibility in configuration, and the ability to store a wide range of items. It is ideal for storing bulky items and can handle significant weight, making it popular in locations such as Riyadh, Dubai, and Qatar.
- Long Span Shelving is designed for heavy-duty storage and can hold significant weight. It can support up to 500 kg per shelf, depending on the configuration. This makes it ideal for businesses in Saudi Arabia and UAE looking for robust storage options.
Yes, Long Span Shelving is highly adjustable. The shelves can be customized to fit different heights and load requirements, allowing for flexible use in storage areas in cities like Dammam and Tel Aviv.
Long Span Racking is typically made from high-quality steel or metal, providing durability and resistance to wear and tear. This ensures that the system can withstand heavy loads and harsh conditions in locations like Kuwait and Jerusalem.
Long Span Shelving is generally designed for indoor use, but with proper treatment, it can be adapted for outdoor storage needs. This makes it versatile for use in various regions, including Qatar and Saudi Arabia.
Long Span Pallet Racking combines the features of Long Span Shelving with the ability to hold pallets. It offers excellent space utilization, which makes it suitable for large warehouses in cities like Riyadh and Dubai.
Long Span Shelving racks offer more durability and higher weight capacity compared to traditional shelving systems. They are perfect for businesses in Saudi Arabia, particularly in industries that require sturdy and reliable storage solutions.
Yes, Long Span Shelving systems are designed for easy installation and can be assembled quickly. Many businesses in UAE and Saudi Arabia appreciate how simple and efficient the setup process is.
Long Span Shelving racks are versatile and can be used across various industries, including retail, manufacturing, and logistics. They are especially common in warehouse settings in Qatar and Tel Aviv due to their ability to hold bulky goods.
Uses of Long Span Shelving
Long Span Shelving is commonly used in warehouses, factories, and retail stores to store heavy and bulky items. It is particularly popular in Saudi Arabia and the UAE, where space optimization is essential.
Yes, Long Span Shelving is ideal for storing tools, machinery, and equipment due to its strength and flexibility. Businesses in Riyadh and Dammam often use it for this purpose.
Absolutely. Long Span Shelving is often used in retail environments to display goods like large boxes, electronics, and furniture. It’s a popular choice in places like Dubai, Qatar, and Jerusalem.
Long Span Shelving is perfect for organizing items in warehouses and logistics centers. It can hold bulk stock and make retrievals easier. In cities like Riyadh and Dammam, it’s commonly seen in distribution centers.
Yes, Long Span Shelving can be customized to fit specific products, ensuring optimal space utilization. This makes it an ideal storage solution for a variety of industries in Saudi Arabia and the UAE.
Yes, Long Span Racking is frequently used in automotive industries for storing car parts and accessories. It’s an excellent choice for businesses in Tel Aviv and Riyadh.
Long Span Shelving is perfect for storing large files and documents. It’s commonly used in offices and archives in Qatar, Dubai, and Kuwait, where organized storage is crucial.
While Long Span Shelving is not specifically designed for cold storage, it can be adapted with special coatings and materials to withstand low temperatures. It is used in some warehouse settings in Saudi Arabia and Jerusalem for cold storage.
In manufacturing, Long Span Shelving is used to store raw materials, tools, and parts. This system ensures efficient organization and easy access, which is highly beneficial for businesses in Dammam and Riyadh.
Yes, Long Span Shelving can be used in residential settings for heavy-duty storage needs, such as in garages or basements. It is gaining popularity in cities like Tel Aviv and Dubai for personal storage.
RELATED PRODUCTS
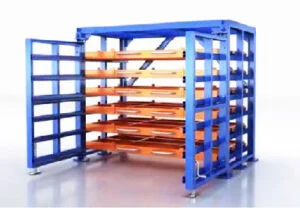
ROLL OUT SHEET RACK
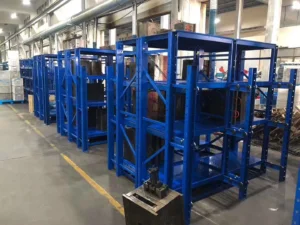
MOULD RACK
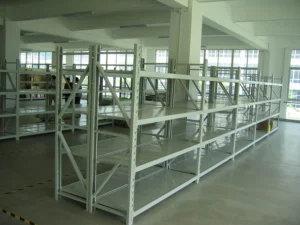
BOLTLESS SHELVING
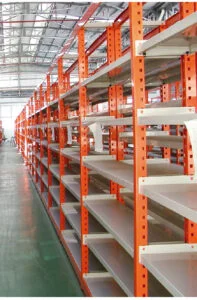
MEDIUM DUTY RACK TYPE A
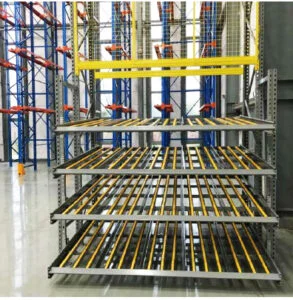
CARTON FLOW RACKING
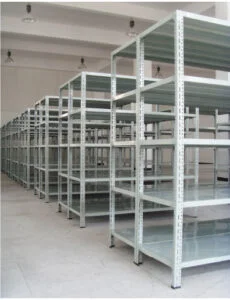
SLOTTED ANGLE STEEL SHELVING
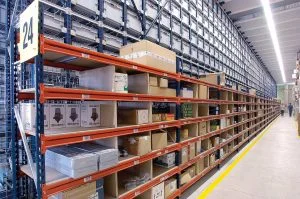